In 2015 CCI embarked on a lengthy process to objectively evaluate the new dry GFRC polymers that were becoming popular. In order to assess the effectiveness of the polymers, it was necessary to first build, test and calibrate an in-house test machine, cast and test many, many samples, analyze the collected data, and finally, interpret those data in order to draw meaningful and helpful conclusions relevant to the concrete countertop industry. This detailed article explains the context, test procedure, test results and recommendations.
The ASTM Test
ASTM C-947-03 “Standard Test Method for Flexural Properties of Thin-Section Glass-Fiber-Reinforced Concrete (Using Simple Beam With Third-Point Loading)” is the test method for determining the flexural properties of GFRC. This testing procedure is designed to measure and calculate three characteristic properties of the GFRC:
- The Flexural Yield Strength (also called limit of proportionality). Yield measures the first cracking of the cement paste.
- The initial flexural Modulus of Elasticity (an indication of how stiff or how flexible a material is)
- The Flexural Ultimate Strength (also called the modulus of rupture). This measures when the concrete physically breaks at the maximum flexural stress it can sustain. (Similarly, with ordinary concrete, the compressive strength “PSI” numbers we’re all familiar with represent the maximum compressive stress the concrete test cylinder can withstand before it crushes.)
The ASTM C-947-03 test requires the use of a deflection measuring device and a chart recorder to produce a force-deflection chart. This chart is used to identify the Flexural Yield Strength and is essential to calculating the Modulus of Elasticity. However, neither the deflection recording device nor the chart recorder is needed to measure or calculate the Flexural Ultimate Strength, which is the absolute strength of the material before it fails.
Why Flexural Ultimate Strength is Relevant
CCI’s flexural testing apparatus included a calibrated load cell accurate to 0.05 lbs and a data recorder which captured the peak load at failure. This peak load at failure represented the Flexural Ultimate Strength of the GFRC being tested. While measuring and recording only the Flexural Ultimate Strength is not in 100% compliance with ASTM C-947-03 as it pertains to Flexural Yield Strength or Modulus of Elasticity, the data collected and the calculated flexural strengths are still 100% valid and relevant to concrete countertop professionals.
While choosing only to measure the Flexural Ultimate Strength of GFRC does provide a limited view of the full properties of GFRC, it indicates the absolute strength of the material, something every concrete countertop maker wants to know. Additionally, measuring only the Flexural Ultimate Strength simplified the construction of the machine, as Modulus of Elasticity measurements require a much more expensive machine. Modulus of Elasticity is a property well known to engineers and is crucial in structural calculations. However it’s not terribly useful piece of information for most concrete countertop makers, as they don’t really have the tools to make use of it in the design of their creations.
Independent Validation of CCI’s Test Results
As stated in our report, multiple identical samples were tested at Applied Materials and Engineering in Oakland California, the same facility that has conducted manufacturer-sponsored testing for at least one of the dry polymers we tested.
To validate CCI’s testing methods and the data collected during flexural testing, multiple samples of various mix designs were mixed and cast all on the same day, by the same person in the same environmental conditions. One bucket of each mix made two sets of samples:
- one set was for testing in NC on CCI’s flexural test machine
- the other identical sample was for testing on Applied Materials and Engineering’s testing machine (which was in full compliance with ASTM-C947-03).
All of the samples were tested on the same day: One set of test samples were tested in NC while the twin set of samples were tested in Oakland, CA.
The flexural strengths for the samples tested in CA by Applied Materials and Engineering were nearly identical to the strengths measured on CCI’s flexural testing machine, validating the results obtained by CCI on its machine, proof that the flexural test results it measured were real and valid.
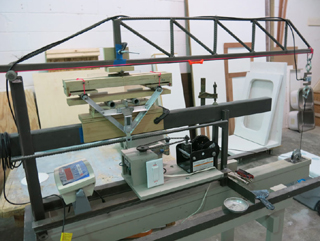
CCI’s Flexural Test Machine
- cross-head movement rate
- loading head and support apparatus dimensions
- bearing design
- loading nose radii, etc
- measuring caliper precision
- sample dimensions and conditioning
CCI’s flexural test program completely satisfied the spirit of ASTM-C-947, which is to objectively and repeatably measure the Flexural Ultimate Strength of GFRC samples. It allowed CCI to rapidly and inexpensively test a broad range of mix designs and ingredients with the full confidence that the results are real, valid and comparable to those obtained from an independent testing laboratory using far more expensive machinery.
Understanding the Scientific Method
Besides the mechanics of testing Flexural Ultimate Strength of GFRC, it is important to understand the scientific method in general. When designing a testing program, first one must determine what exactly is being tested, and eliminate other variables that could confound the test results. A Control Sample or Control Group must be designed to eliminate these other, non-relevant variables.
In this case, the variable being tested was the polymer. The goal of the test was to determine whether dry polymers achieve similar flexural strengths as wet polymers in GFRC. It is well known from decades of research that the addition of wet polymers to GFRC function to eliminate the need for a 7-day wet cure. At the most basic, simplified level, this is apparent because GFRC made with wet polymer and dry cured achieves similar flexural strengths to concrete made with no polymer and wet cured for 7 days. The “Control Sample” is the concrete made with no polymer and wet cured for 7 days.
It is also well known that using too much water in concrete is detrimental in many ways, and a low water/cement ratio is beneficial. This is a variable that must be eliminated in any test that is trying to measure other factors (such as the effectiveness of wet polymer). If the tests to determine whether wet polymers work had used a Control Sample with a 0.40 w/c ratio, whereas the wet polymer samples had w/c ratios of 0.30, the whole test would be invalid. That Control Sample does not eliminate all other variables besides the polymer. ANY concrete made with a 0.40 w/c ratio is going to be inferior in many ways to concrete made with a 0.30 w/c ratio.