Selecting the right diamond polishing pad (or disc) is the key to getting a good finish for your concrete and getting the most bang for your buck.
There are many different sources, names, styles and prices for diamond pads on the market. This can be very confusing, and what often happens is selection comes down to price. This is unfortunate, because in many cases a cheap pad will cost you more in the long run. However, I’m not suggesting we all go out and spend $100 per pad either. There’s a place for those, and we don’t need to go there (granite folks might though).
Choosing the right pad starts with assessing what you plan on doing with it.
- Are you using it for heavy stock removal?
- Is it for general honing?
- Are you polishing the concrete to a high gloss?
Each of these tasks will influence the choice in pad. I’ll outline some of the variables to consider and then create a general template for selecting the right pad for the right task.
Size
Larger diameter pads (e.g. 7″) are much more stable on large, flat areas than smaller diameter pads (3″ and 4″). However, larger pads become unstable on narrow sections of concrete. A 7″ diameter pad won’t stay flat or cut evenly on a 3″ wide strip of concrete. They are also difficult to use on the vertical edges of countertops.
Small diameter pads are less stable and more likely to gouge when processing large areas on a big polisher, but with a smaller polisher (espcially a pneumatic polisher) they work very well for processing edges and narrow sections.
A good all-around size is a 5″ diameter pad. Many low-cost polisher package deals come with 4″ pads. These can be difficult to control with hand held polishers on concrete. Smaller 4″ pads are really meant for use on hard stone, which is much less prone to gouging than concrete.
Thickness
Diamond pads come in a variety of thicknesses, from around 2mm thin to 8mm thick.
Thicker pads will last longer, but thicker pads are stiffer, and sometimes are prone to cupping when they dry.
Thin pads don’t last as long (especially when aggressively cutting), but they are more flexible. This is a big advantage when honing or polishing inside curved integral sinks.
Pattern
The pattern molded into the cutting surface plays a significant role in the lifespan and the cutting quality.
Often pads used for coarse honing (30 and 50 grit) have an aggressive, open pattern with wide and deep channels. Pads with large, open channels allow the abrasive cutting residue to be ejected quickly and effectively. This increases the lifespan of the pad when aggressive stock removal is performed.
Pads that have many narrower channels are best only for polishing (400 to 3000 grit), where almost no stock is removed. Narrow channels clog more readily when aggressive cutting is performed and when insufficient water flows out from under the disc.
A good balance of these factors is lots of channels that are large in proportion to the diamond-covered surface. This provides flexibility to the pad while still allowing for effective ejection of cuttings and a large proportion of diamond area. In contrast, pads with very large channels and very large “islands” of diamonds tend to be inflexible.
Diamond Quality
While it’s very easy to see the thickness and channel pattern in a diamond pad, it’s nearly impossible to assess the quality of the diamonds used in the pad, or for that matter, the grading and quantity of diamonds. Ultimately it’s the diamonds that do the cutting, and they are what makes a pad expensive. The better the quality of diamond, the better the grading and the more diamonds in the pad, the more expensive the pad will be.
It’s possible to find $1 pads and $100 pads that look almost identical. What’s not visible are the diamonds, and that’s where you need to trust your supplier to inform you of what you’re getting.
The most expensive pads use the best industrial diamonds. The diamond concentration is high (each manufacturer optimizes the quality and quantity of diamond in their pads), and the gradation is narrow. Like sand and gravel, diamonds come in a variety of sizes. A narrow gradation means almost all of the diamonds are about the same size, so the grit number of the disc is a more precise description of the diamond size gradation. Any variation tends toward smaller diamonds, which don’t affect the quality of the concrete surface.
Cheap pads use low grade diamonds. These tend to have more flaws and much poorer gradation. In addition, fewer diamonds may be used in the pad. Often the gradation is broader, so a 100 grit pad may actually have significant amounts of smaller diamonds and some coarser diamonds (like 70 grit). This results in a lower surface quality (more scratches) and slower cutting (because there are more smaller diamonds in the pad).
Binder
The binder that encapsulates the diamonds is just as important as the diamonds, and it has a profound effect on the performance and longevity of the pad. Binder materials range from ceramic to resin, and different materials are used for specific applications. Binder hardness is important. A binder that’s too soft will wear away quickly when processing an abrasive material like concrete.
Nearly all wet polishing pads use a resin binder, and resins vary. It’s very rare that a pad distributor will describe the binder with any meaningful detail, so here personal observations and reliance on trusted recommendations are necessary to make a good choice. Too often the least expensive pads use soft resin binders that wear away quickly. If you end up using three times as many pads as you would with a pad that costs twice as much, you are not saving money in the end.
Ceramic binders tend to wear better and stand up to higher temperatures than resin pads. Many dry pads use a ceramic binder, which helps to prevent the smearing and glazing that can occur when a resin based dry pad is run at a speed that’s too high.
Recommended Diamond Pads for Concrete Countertops
The Concrete Countertop Institute has developed diamond pads specifically designed for concrete countertops, not granite and not concrete floors.
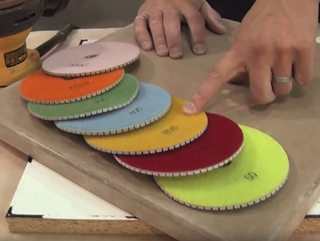