I’m often asked whether dry grinding the concrete can be used to prepare the concrete surface for Omega Concrete Countertop Sealer, Ovation Concrete Countertop Sealer<, or any coating sealer.
The answer is NO.
Dry grinding is not the same as wet grinding, even with the same grit. Dry grinding/polishing tends to burnish the concrete surface, making it too smooth for good sealer adhesion. This applies to any coating sealer, not just Omega and Ovation.
The practice of dry sanding concrete using dry sandpaper is often seen as being simple, fast, easy, and “gentle” to the concrete. Unfortunately, this practice also has a downside that isn’t obvious until it’s time to seal the concrete.
Dry sanding tends to burnish the surface. This means that instead of uniformly abrading the surface to reveal a pristine, fresh and uncontaminated surface, dry sanding often leaves the surface smoother and shinier than it started out as.
In addition, contaminants like wax and form release agents that were picked up from the mold during casting tend to be worked into the concrete surface instead of being abraded away.
The result is concrete that is usually too smooth, and possibly contaminated too. Both conditions can lead to sealer adhesion failure.
[caption id="attachment_16680" align="aligncenter" width="750"] Burnishing from dry diamond pads (200 grit, left), and regular sandpaper (220 grit, middle and 80 grit, right). Un-sanded concrete is the lighter area on the far left side of the concrete.[/caption]
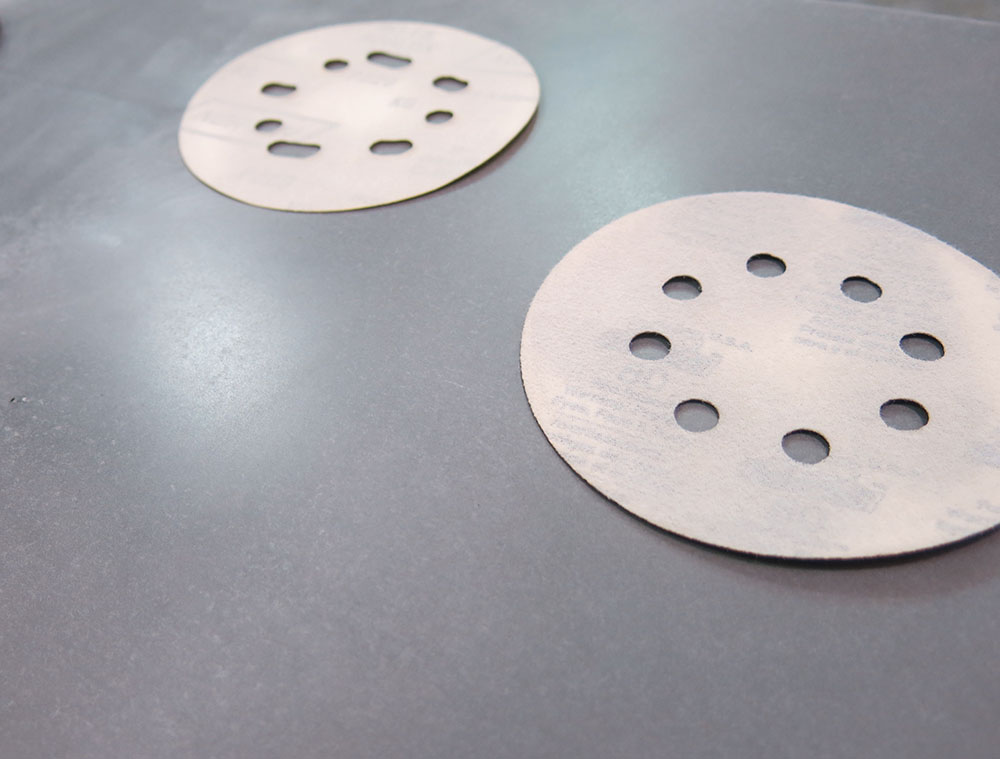
Burnished sheen from 220 and 80 grit sandpaper.
The reason dry sanding tends to both burnish the concrete and work contaminants into the surface has to do with the sanding process. Most sandpaper used is meant for wood, though some is also sold for metal. The abrasive grains tend to be a bit harder than concrete (or a lot harder, depending upon the concrete’s age), so sanding will create dust and grit. This dust and grit tends to get trapped under the sanding pad, and both the sanding abrasive particles and the concrete grit act on the concrete surface. If there is inadequate dust removal under the sanding pad, the grit and abrasive particles will soon start to polish the surface instead of cut into it, since the concrete dust and grit are the same hardness as the surface. Contaminants are usually on the surface of the concrete, and if only the top surface is abraded and burnished, with inadequate dust clearing, then the contaminated dust gets ground back into the surface, creating bonding issues for your sealer.
Dry polishing with diamond pads on an electric or pneumatic polisher creates concrete cuttings which don’t get flushed away like they do with wet polishing. Because the powdery cuttings tend to remain under the polishing head longer, they break down and act as finer polishing media. This is why dry polishing is more effective than wet polishing when trying to polish concrete to a mirror shine, because the concrete cuttings themselves act as a finer polishing compound than the diamond pad that created them.
Additionally, the super-fine cuttings get forced into the open concrete surface pores, contaminating the surface, and that can cause adhesion failure.
Here is a detailed video showing how dry grinding burnishes the surface:
What if you dry sanded your concrete and now want to seal with Omega or Ovation?
All is not lost, and you’re not faced with a huge task either.
Omega and Ovation (and all high performance coatings) relies on a slightly rough surface microtexture to create a strong and permanent bond with the concrete. As such, dry sanding (and even dry polishing with diamonds) prevent what is necessary for sealer adhesion.
If you’ve dry-sanded your concrete and still have a cement-cream finish, then the easiest thing to do is to wet sand by hand using 320 to 400 grit silicon-carbide wet/dry sandpaper. Silicon carbide is much harder than concrete, so it abrades the surface easily, but won’t remove your cream finish. And since it’s a fine, even grit, 320 won’t leave deep scratches that will show through the sealer. Wet sanding helps flush the cuttings, and it prevents the frictional heating that can lead to smearing and burnishing. Be thorough and make sure the entire surface is evenly sanded.
If you’ve dry sanded your concrete and it has exposed sand grains or decorative aggregate (like glass or stone), then you will need to abrade the much harder aggregate with something more aggressive than sandpaper. The simple and fast way to do this is to use a wet diamond polishing disc (100 grit or 200 grit) attached to a regular random orbit sander. Simply spray some water on the concrete to get it wet, and “sand” the surface using the diamond disc to abrade away the burnished surface. Be very thorough, as random orbit sanders are not nearly as aggressive as wet polishers. Done properly, this will give you a surface that will permit Omega to bond tenaciously to the concrete.
Here is a video about the process (in the context of removing an existing coating and resealing with Omega):