This article was originally published in Concrete Decor Magazine here, but we wanted to share it with you as well because we believe it’s valuable reading!
Forming Concrete Countertops
Successfully forming concrete countertops and other creative architectural concrete elements involves common woodworking techniques, sculpture, careful planning and a touch of mental gymnastics.
We ask a lot from something as humble as a box. The forms or molds we build for our concrete creations are the devices that create the shape and texture of the concrete we make. Without molds, our concrete would be shapeless.
Forms serve many functions beyond simply containing the concrete. The formwork defines the precision and, to some extent, the quality of the casting. Well-made forms create straight lines, fair curves and right angles and lead to easy, effortless installation. Good forming techniques can increase efficiency, boost the bottom line, and reduce the amount of material we use and discard. And finally, formwork is often the vehicle by which we explore and satisfy our creativity, for the forms are also things we make with our hands.
Forming basics
The most basic formwork we use is a simple rectangular box with four sides and a base plate for the foundation. The construction process to determine size and shape starts with a template for a kitchen countertop, or a drawing or set of plans for a piece of furniture or freestanding island. Generally, the base plate is the exact size and shape of the finished concrete piece.
The size of the completed box is determined by the desired thickness of the slab, the thickness of the forming material and how the sides are fastened to the box. For example, most melamine is ¾ inch (or 0.75 inch) thick, or 19 mm thick. If a countertop is constructed to be 2 inches thick, then the interior of the forms are 2 inches deep, but the four sides that form the walls of the mold are 2.75 inches tall. This means that the sides wrap around the outside of the base plate, and this permits the sides to be easily attached with screws drilled in perpendicularly.
Alternatively, the base plate can be made larger than the desired piece and the sides attached on top of it using pocket-hole joinery.
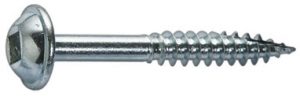
A pocket-hole screw
Pocket-hole screws are special wood screws used in pocket-hole joinery. However, these versatile screws can also be used for normal fastening. What makes them useful is that the underside of the head is flat. No countersink is needed, and overtightening the screw only strips out the drilled hole, whereas overtightening a normal flat-head screw (that has a conical underside) will crack the formwork.
Note that even though these screws are self-tapping, it’s still important to predrill the formwork. Driving a screw into undrilled melamine will cause the material to bulge or split. Bulges in the melamine surface will create dimples in the cast concrete surface. These will be very evident if they occur along the front edge of a countertop.
To use the pocket-hole technique, you first use a jig to drill the pocket-screw hole, as shown in this photo:
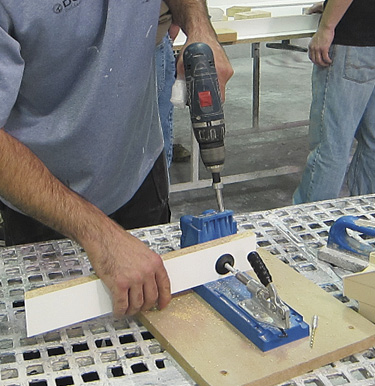
Using a jig to drill the pocket-screw hole
The larger photo at the top of this page shows a completed form using the technique of attaching the sides on top of an oversized base plate, using pocket-hole joinery.
Forming materials
What the forms are made of is influenced by a variety of factors, not least of which is the final appearance that the customer requests. The choice of forming material, and the process and care by which the forms are assembled, is both influenced by and significantly affects how the finished concrete looks.
The precision and quality of the formwork for a cement cream finish are different (and greater) than that needed for exposed aggregate concrete. Balancing the needs for flawless formwork and speed, reusability and economy are the convoluted path we all navigate when deciding what our forms are made of and how they’re built.
With few exceptions, two prime characteristics that are important for most formwork materials include being waterproof and being nonreactive with the concrete. The formwork should neither change nor deform during casting or after it hardens. It should maintain the desired shape under the weight of the concrete during and after casting. Other beneficial characteristics are availability and strength.
Melamine
Forms can be constructed from a wide variety of building materials, and one of the most commonly used is melamine (which refers to the hard, waterproof coating applied to particleboard). Melamine is used in cabinet construction, often for the carcass and shelving.
The upside of melamine is that it’s cheap, readily available and works well for many applications. One of its major downsides is that its particleboard core, which gives the sheets structure, is moisture sensitive. That makes building the forms — and waterproofing the seams — important.
Moisture lost from concrete will create discoloration, where the water-to-cement ratio of the cement paste drops near the leaky seam, and the concrete in that zone cures a different shade (often darker). Also, moisture that’s absorbed by the particleboard causes the core to swell. Sometimes the swelling occurs faster than the concrete sets and gains strength, so the swollen formwork distorts the concrete while it’s setting.
The other downside of melamine is its lack of durability. If the hard coating gets scratched, moisture can penetrate and cause the moisture problems noted above.
Steel
Steel is often used for multiuse formwork, usually as steel-topped casting tables, but also steel angle-iron as edge forms. Using steel for formwork works best when you’re not trying to achieve an as-cast cement cream finish. Exposing aggregate naturally removes the surface texture during the grinding process, as does honing to create a salt-and-pepper finish.
Steel can be hot-rolled, cold-rolled, plain carbon or stainless. Cold-rolled steel is better for concrete that doesn’t need much post-cast processing, because the steel has better dimensional tolerances and it has a smoother surface texture. Hot-rolled steel is suitable for concrete that will be honed or will have exposed aggregate, because hot-rolled steel still has the mill-scale (the dark grayish-blue surface) left from the steel mill. This leaves a more textured surface on the concrete.
Both stainless and plain carbon steel require a form-release agent. Many commercial form-release agents designed for steel incorporate an anti-corrosion agent that keeps bare steel from rusting. Plain-carbon steel will rust if left unprotected, but is cheaper than stainless steel.
Foam
Foam is a versatile and common forming material, particularly insulation foam (usually pink or blue in the U.S.). Because it’s fairly dense, it can be easily cut, sanded, routed and shaped. It makes a great material for curves, blockouts and custom-edge moldings.
Foam is a very good material to use for undermount sink blockouts. It’s rigid enough to withstand the pressure of fresh concrete, but soft enough to be easily removed after casting without fear of cracking the concrete during blockout extraction. Some people wrap smooth tape around the outside of the foam blockout to achieve a glossier cast surface, and others leave the foam bare.
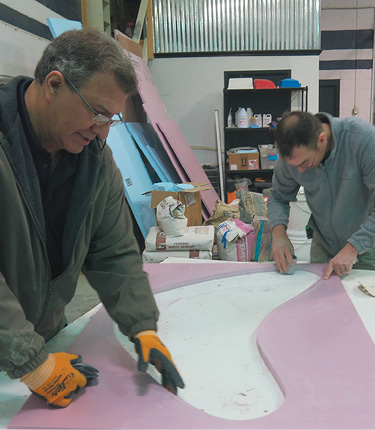
Foam can be used to create a curved table top form. The concrete will be cast inside the hole in the foam.
Forming curves
Curves in concrete can be formed in various ways. Foam can be cut and sanded to nearly any shape, so in that respect it’s very versatile. But foam sheets only come in certain thicknesses, and while gluing and stacking foam to create thicker sections is possible, dealing with the gaps and seams between the layers is more challenging.
Flexible strips of thin material can be bent into an arc. Melamine will bend to some degree, but tighter curves may require plastic. Laminate is a good material to bend, but it requires a backer material for support. Often bendable plywood or even foam provides the support to keep the thin laminate sheet in alignment. Or, the laminate can be secured to rigid side plates using 2-by-4 spines placed behind the laminate sheet.
Good plastics to cast against include acrylic, polycarbonate, laminate, high-density polyethylene and polystyrene, among others. Usually plastic yields smooth surfaces that require little or no processing.
Conclusion
Other forming materials include rubber, fiberglass, high density overlay and formply. A complete explanation of every possible forming material and technique would take an entire book. The most important ingredients for success with forming countertops and other architectural concrete elements are precision and creativity. “Think outside the box” when creating your form “boxes”!
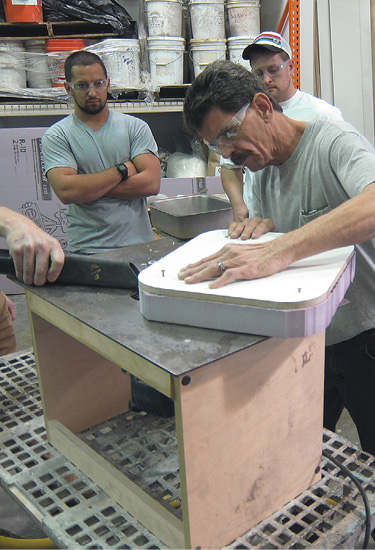
Here, class participants shape a foam sink knockout on a router table to fit a wooden sink-hole template.
More Information
For more information on forming concrete countertops (as well as every other step in the process!) see our professional training.
- Learn all of the technical aspects of how to make concrete countertops in this self-study course.
- If you also want to learn all of the business aspects of marketing and selling concrete countertops, see this self-study course.
- Our Ultimate Concrete Countertop Training provides all of this information along with 5 days of hands-on learning and lifetime support.
- Want to learn advanced forming techniques? See our self-studies on this topic.