In the last article, I discussed how PVA fibers are used in engineered cementitious composite concrete (ECC). Today I’d like to review some of the many types of fibers that you can use when making concrete countertops and some of their purposes, as well as explain which types of fibers are appropriate for which method/mix:
- Traditional precast
- GFRC
- ECC
Why are fibers added to concrete?
Fibers are used in concrete for a variety of reasons, but not all fibers do the same thing or have the same effect. They can be used for reinforcing or can be used to prevent shrinkage and cracking.
- When fibers are used for improving the flexural/tensile properties of the concrete, this is known as primary reinforcing.
- When fibers are used for plastic shrinkage control, and to prevent crack creation and propagation in the cement matrix by bridging the microcracks, it is known as secondary reinforcing.
The choice of what fiber to use depends upon a variety of factors. In commercial construction, cost is often the primary factor, as most fibers are used for secondary reinforcement reasons. For concrete countertops and other creative concrete applications, the cost of the fiber is often less important than the effect of the fiber on the concrete’s performance and on its appearance.
Additionally, different mixes are best suited for different fibers. GFRC fibers must be used in high volumes, so the mix is built around a specific fiber used in a specific dose. ECC is the same way, but with different mix proportions and very different fibers.
The takeaway here is that fibers are not generic ingredients that can be plugged into any mix without considering the benefits those fibers can bring and their effect on the concrete’s workability.
Fibers as Primary Reinforcing
Most fibers used in most types of concrete don’t provide any benefit to boosting the tensile strength of the concrete. These tend to include cellulose, polypropylene, nylon, and other common types of “stealthy” fibers. Only certain types of fibers can, and these must be carefully matched with a tailored mix design built around the type and amount of fiber used in the mix. GFRC and ECC are two examples of specialized mixes that use specialized fibers.
Fibers as Secondary Reinforcing
As the concrete sets and transforms from a workable paste into a hard solid, plastic shrinkage can occur. This is especially true in concrete slabs exposed to heat or wind. The matrix of fibers helps to stabilize the wet concrete and distribute the shrinkage stresses so that large cracks are minimized or eliminated.
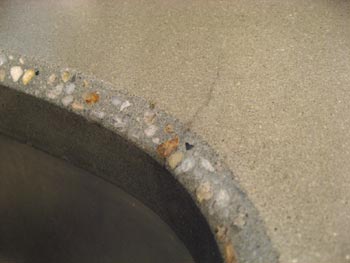
Fibers can help reduce shrinkage and cracking.
Fibers can also help combat shrinkage by spreading the tensile loads across the concrete. The fibers act as a net, in this case holding small cracks together and transferring stresses across cracks into adjacent concrete. This helps keep any cracks that appear small, often too small to even see. Rather than having one or two large, highly visible cracks, you’re left with a series of small, hard to see cracks spread across the slab.
What are concrete fibers?
Fibers in precast concrete countertops can play a valuable role in both boosting primary reinforcing and providing secondary reinforcing. However, the type of fibers and the methods used will vary depending on which type of reinforcing you’re after.
Most commonly used fibers are synthetic, either polypropylene or nylon, but some are natural, like cellulose fibers. Let’s dive into a few of your fiber options. Remember, this is not an exhaustive list!
Polypropylene or Nylon Fibers – Polypropylene and nylon fibers are used for shrinkage control; they add no structural tensile strength to the concrete. These fibers play a valuable role during the curing process but provide no benefit after. They simply stretch too much to provide any resistance to tensile stresses.
Polyvinyl Alcohol (PVA) Fibers – PVA fibers have some structural strength and can also be used for shrinkage control. While they cannot replace reinforcing steel, they improve the mechanical properties of cured concrete, boosting its strength. These are the best choice when the fibers cannot show at all. However, caution must be used because these fibers are so fine, very small volumes can choke the mix. They are an important component of ECC (see below).
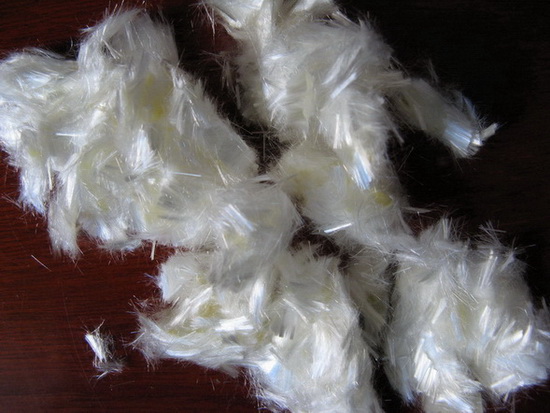
PVA Fiber for Concrete Countertops
Alkali Resistant Glass Fibers – AR glass fibers are the type of fiber primarily used with GFRC (see below). They can also be used to provide primary and secondary reinforcing in traditional steel reinforced concrete countertops. These fibers are special glass fibers that won’t break down, even when in contact with alkaline concrete. They will show in traditional precast, however, and are not commonly used.
Other Fiber Choices for Precast
Some fibers are strong and can provide adequate structural strength, but the material they’re made of doesn’t make them a good choice for concrete countertops. They are primarily in large industrial concrete projects.
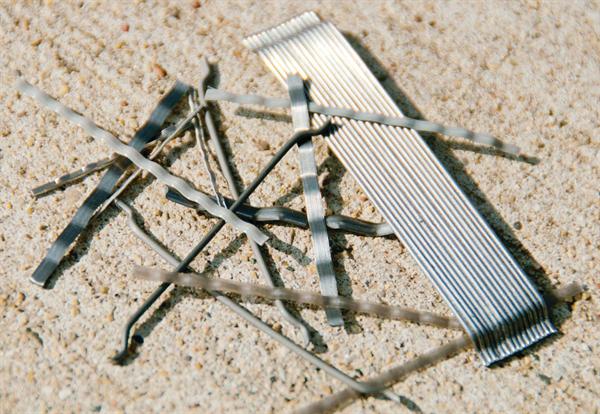
Hooked Steel Fibers
Hooked Steel Fibers – Hooked steel fibers possess structural strength. They can help to distribute tensile stresses across the countertop. However, they are large, ugly and will show.
Chopped Carbon Fibers – Chopped carbon fibers have stiffness and strengths equal to or greater than steel. Reinforcing is still needed, but the fibers provide a helpful boost of strength and minimize shrinkage during the curing process. But because they are black, carbon fibers will show definitely show in most concrete that’s not black or very dark.
Fibers used for GFRC
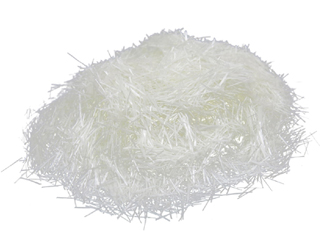
AR glass fibers for GFRC
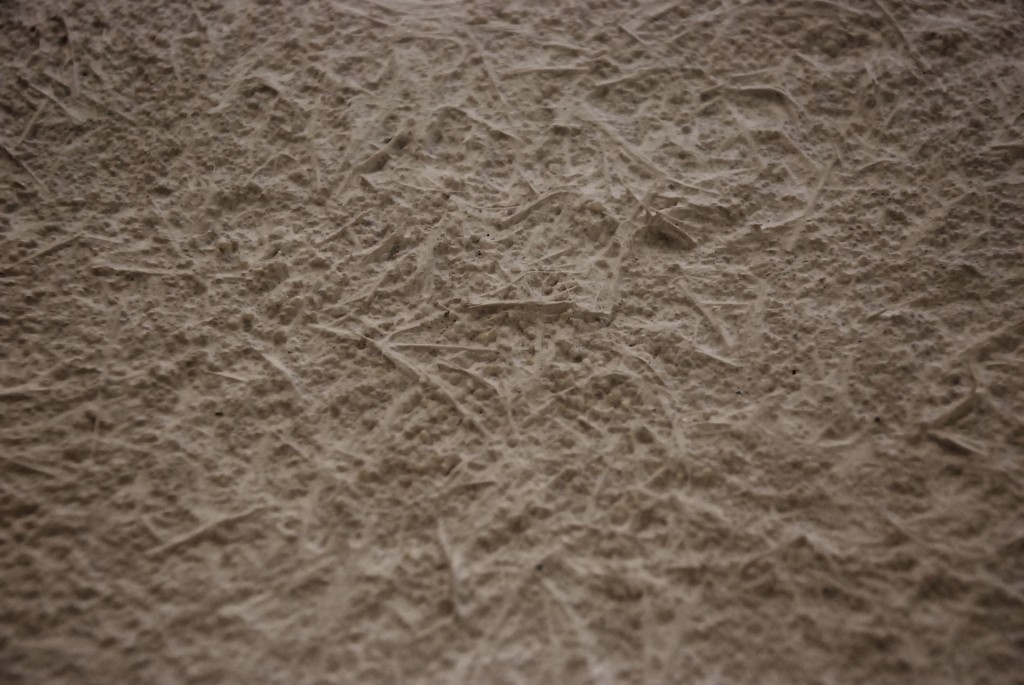
Properly Aligned Fibers in GFRC, Resulting from Thin Layer and Rolling
GFRC utilizes both specialized concrete and strong AR glass fibers. Both possess benefits on their own, but when combined they become something amazing. The tensile strength helps GFRC to resist pulling apart forces while the flexural strength helps it to resist bending. The glass fibers and the high polymer content of GFRC provide these unique properties that are essential to a long lasting concrete countertop.
Rather than using steel for reinforcement, GFRC relies on these glass fibers to prevent cracking and breakage. Making GFRC isn’t as simple as just adding some fibers to your concrete mix design. The size, shape, material, and amount of fibers used has a significant effect on the concrete. Using the wrong type of fiber, or not using enough, can lead to disappointment and a failed concrete countertop.
Because AR glass fibers are used in such high volumes in GFRC in order to provide the necessary strength, they would be extremely visible if a veneer coat without fibers were not used. This fiber-free veneer coat is called a mist coat or face coat. It has no strength and is solely for aesthetic purposes.
For more information about GFRC, please see this index of GFRC articles and videos.
For high performance AR glass fibers with excellent flowability, see Integrity UltraFibers.
Fibers Used in ECC
As explained in the last article, PVA fibers are used in ECC to provide both structural strength and shrinkage control. The combination of well-dispersed, micro PVA fibers and the strong, fine-grained homogeneous matrix is what results in the amazing ability of ECC to bend and crack without losing strength. Because of the highly dispersed microfibers, cracks tend to be small, and sometimes even invisible.
Recommendations
There are many different types of fibers used for different reasons in the various methods of creating concrete countertops. My recommended usage is:
- Precast: For the type of precast concrete we make, you may optionally use acrylic, nylon and PVA fibers, at a dose of 0% to 0.5% of total mix weight. This is only for secondary reinforcement and plastic shrinkage cracking. It does not replace primary steel reinforcing. Higher doses can choke the mix – essentially turning it into a big hairball!
- GFRC: Use AR glass fibers, 3% of total mix weight, properly compacted. GFRC is not GFRC without AR glass fibers as a replacement for primary steel reinforcing. (See this article.)
- ECC: ECC is a complex composite of PVA fibers, 1% to 2% of total mix weight, in a properly engineered mix utilizing very fine aggregates. It is impractical to prescribe a DIY recipe for ECC due to the complexity of the mix design.